Demystifying Hot Melt Adhesives: A Comprehensive Guide
Contrary to what many believe, hot melt adhesives and hot melt technology have progressed far beyond the crafting and DIY industries. For new or inexperienced users of hot melts, it can be confusing trying to work out all the variables involved, and how to get the best from these adhesives.
In this blog, we’ll explore what hot melt adhesives are, what to consider before using them, and some tips to get the most out of the technology.
What is a hot melt adhesive?
A hot melt adhesive, or hot melt glue, is a type of thermoplastic adhesive that’s applied in a molten state and solidifies upon cooling to form a strong bond between two substrates.
They’re typically made up of a base polymer to which other raw materials are added. This polymer acts as the framework on which the adhesive and its properties are based. Other raw materials that may be part of the final formulation include tackifiers in the form of resins, waxes that adjust variables such as surface tack and viscosity, and additives to give the finished adhesive more stability.

Unlike many other forms of adhesive, hot melt adhesives are 100% solid materials with no solvents. At room temperature, they are safe to handle and, in many cases, have a near-unlimited shelf life. They’re also able to be remelted and set several times without compromising their adhesive properties.
Hot melt adhesives are commonly used in the packaging, woodworking, product assembly, and crafting industries, but they are also prevalent in the automotive, construction, and electrical sectors.
What factors affect hot melt choice?
Much like other adhesive systems, hot melts are not universally applicable and aren’t a ‘one size fits all’ solution. Although many formulations are classified as general purpose, there are specialised grades tailored to distinct applications and substrates.
These specialisations range from different viscosity levels for better gap-filling or tighter joins, to extended or shortened working times tailored to how quickly the bond needs to be formed.
For these reasons, it’s important to understand the following factors:
- What materials are you bonding? How do they react to high temperatures?
- How long after application do you need the adhesive to stay “tacky”?
- Is it preferable to have a thicker or thinner adhesive bead?
- Do you require an instant set when the materials are brought together, or do you need time for adjustments?
- Will the final bond be under any extreme temperatures? Both high and low.
- Will the final bond be visible, or does it need to blend with the materials to which it’s bonding?
- Does the final bond need to have some flexibility?

If you can answer all of the above questions, you’ll be able to specifically search for your perfect hot melt adhesive.
Hot melt or Low melt?
Closely linked to factors that affect your hot melt choice, there are a range of hot melt adhesives specifically formulated for use with heat-sensitive substrates.
Regular hot melts are designed to run at temperatures exceeding 160°C (320°F). At these temperatures, sensitive materials such as plastic films, expanded polystyrene and many foams will melt or burn. For these substrates, a hot melt which functions at a lower temperature is required.
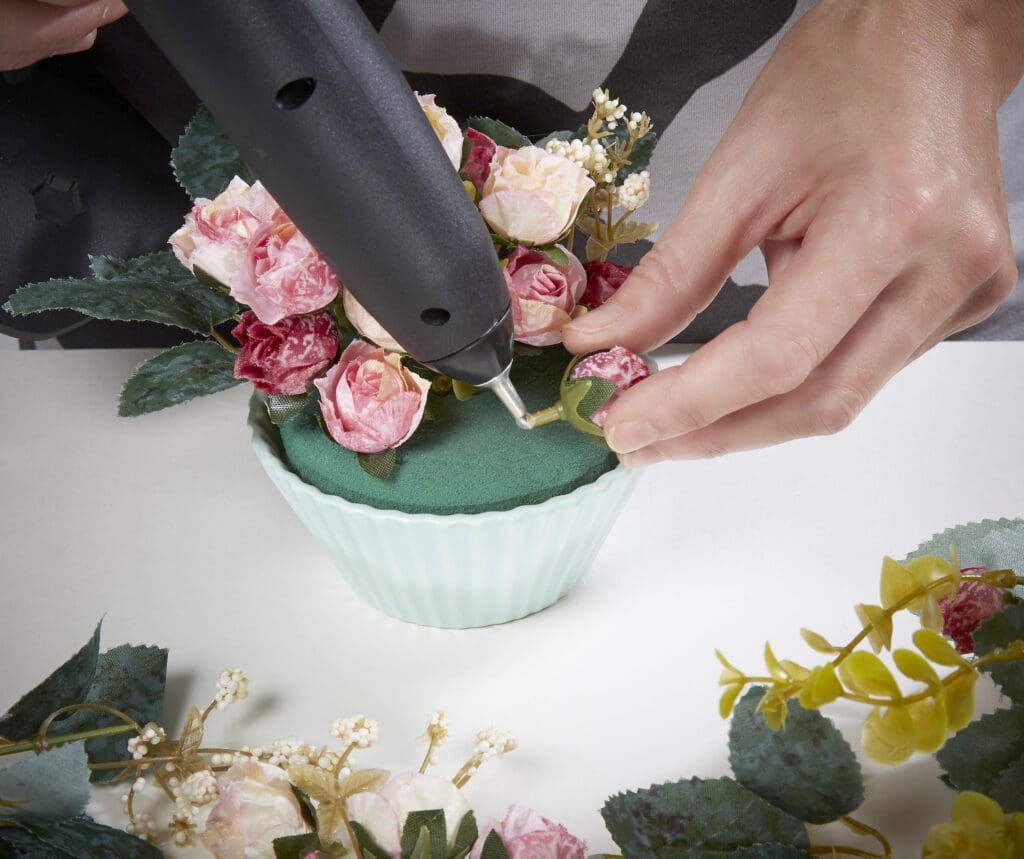
This is where low melt adhesives excel. These are specially formulated to maintain the same adhesive properties as their hot melt counterparts but are dispensed at much lower temperatures (120°C to 130°C or 250°F to 265°F).
So, before you look at buying a certain glue gun or hot melt adhesive, you should consider what materials you’re bonding, and whether you will need hot or low melt systems.
For a better understanding of hot melt adhesive grades and their chemistry, check out our Tecbond adhesive guide, which outlines our most popular hot melt adhesives and their specifications.
Application Method
Once you’ve decided what kind of hot melt you require, you can then join this choice with the most suitable application method.
The most common application method is a hot melt glue gun or glue applicator. As well as being the easiest to use, glue applicators are available in a variety of different models to best suit the application. These variations include:
- Adhesive size (12 and 15mm sticks and 43mm slugs)
- Melting/output temperature
- Melt rate and output (linked to adhesive size)
- Corded or cordless
- Application form (bead or spray)
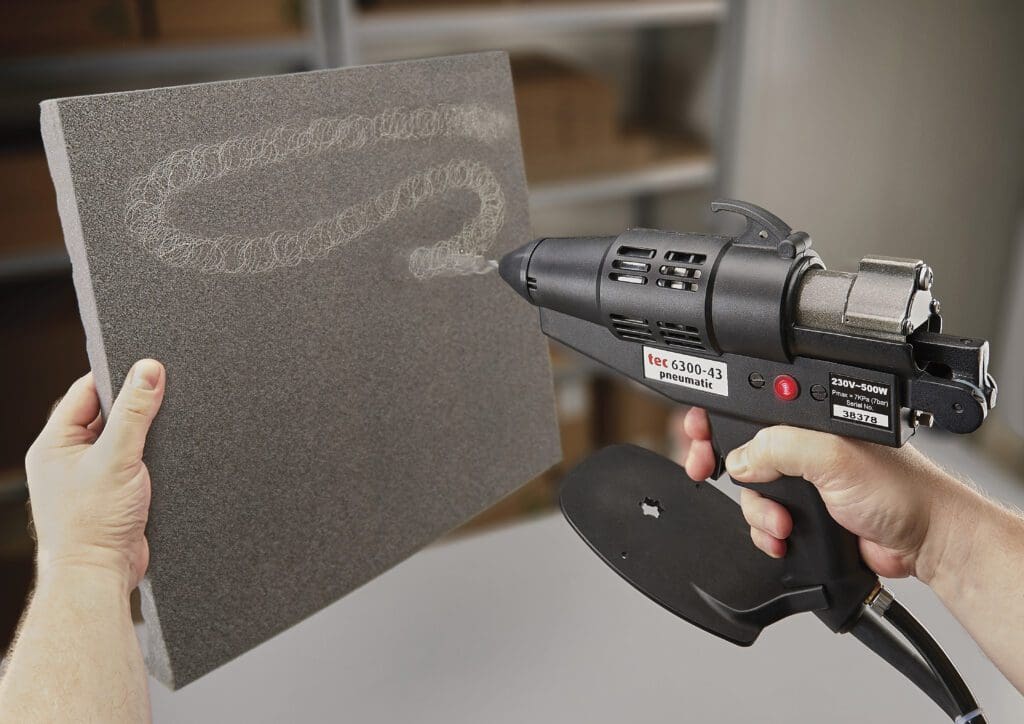
The biggest benefits of hot melt glue guns are their speed and precise control. With warm-up times of around five minutes or less, and the ability to control how much hot melt is dispensed with each pull, they’re the go-to choice for most users and industries.
The other common application method is bulk machinery. This application method is more common in fast-paced industrial environments where processes are automated, such as packaging and assembly lines. Bulk machinery tends to have much higher output and can operate all day with minimal to no downtime.
These machines work by having a tank filled with molten hot melt that is kept at a constant temperature. This molten hot melt is then dispensed automatically when required. The drawback to these machines is their high price and lack of portability.
Before choosing an application method, it’s important to understand if the hot melt you wish to use is compatible and the best fit. Certain hot melt formulations will work better with tools that run at a higher temperature, while others are available in formats that better suit bulk dispensers than glue guns. Always refer to technical data sheets for both the hot melt adhesive and applicator before making a purchase.
If you’re using a Tecbond formulation and Tec glue applicator, you can refer to our Tec glue gun guide, which details each applicator.
Tips for using hot melt adhesives
As with any adhesive technology, some best practices will ensure you get the most out of your hot melts.
- Ensure your hot melt stick or slug is clean and dry before inserting it into your applicator – Moisture can not only potentially damage the internal components but also affect the adhesive qualities.
- Ensure the hot melt isn’t misshapen – This can cause blockages in the applicator, leading to adhesive meltback.
- Don’t leave glue guns on and idle for extended periods – Despite not being in use, the internal heating system will continue to melt adhesive currently in the glue chamber. This can lead to nozzle leakage or adhesive meltback.
- Do not exceed recommended application temperatures – Running adhesives above recommended temperatures can cause burning or charring, as well as changing properties such as viscosity and open time.
- Use the correct amount of adhesive – Don’t be tempted to over-apply adhesive. Not only will larger amounts of adhesive increase open time, but it may negatively affect the substrate you are attempting to bond (saturating a very porous substrate for example).
Conclusion
In conclusion, hot melt adhesives offer a versatile and efficient solution for bonding different materials across a wide range of industries. As we’ve explored in this comprehensive guide, understanding the composition, application methods, and factors influencing the choice between hot melt and low melt adhesives is crucial for achieving optimal results in your projects.
Leave a Reply